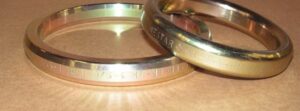
The American Petroleum Institute (API) first issued its standard for Ring Joints and Ring Joint Flanges (API Specification 6B) in June of 1936. This standard (which was adopted by the American Standards Association into the 1939 edition of ASA B16e) had two different groove profiles for ring joint flanges. Flanges under 6” had a round-bottomed groove and could only use oval rings. Note that the ring did not contact on the bottom of the groove, but had a wedged contact on the tapered side of the grooves, as is still the case. The oval style of ring joint gasket was the only option for flanges under 6”. Flanges 6” and over had a flat-bottomed groove which could use either oval or octagonal ring joints.
Over the years changes were gradually introduced, so that when the 1957 edition of ASA B16.20 was published, the only groove profile was the flat-bottomed one, and octagonal ring joints were available for all sizes. This change allowed the oval or octagonal gasket to be used in new (or retrofitted) installations, whereas the oval gasket was still required in existing applications that had the earlier groove design. Undoubtedly, the fact that the octagonal gasket could not be used in some of the pre-existing flanges was a barrier to its acceptance.
Both gaskets seal by wedging tightly into the sides of the groove as they are compressed. However, the octagonal gasket has a broader sealing contact surface, as the entire 23-degree-tapered edge of the gasket ring is in contact with the mating groove face. (See drawing.)
While it is generally recognized that the octagonal ring gasket is a superior design that offers higher sealing efficiencies and reliability, oval gaskets still comprise about 90% of the market. The three factors that most likely account for this surprising fact are:
- Universality. As noted, the oval gasket will fit into all standard ring joint flanges. However, as the old round-bottom flanges become rarer, the universality of the gasket becomes less of a benefit.
- Inertia. Long-lived habits die hard. Many of today’s industrial specifications are rooted in earlier specifications that were written when the change was being made from rounded grooves to flat-bottomed grooves. The influence of those early decisions still exists – even though the rational they rested on is largely gone.
- Price. Most manufacturers charge a 15-20% premium for the octagonal gasket, as there are more surfaces to machine.
The deficiencies of the oval gasket primarily arise from its small point of contact with the flange groove. The oval cross-section generates a single-point contact ring with the flange. The narrowness of this contact results in very high seating forces. Even though the gasket is supposed to be softer than the flange material, both the gasket and the flange see some deformation as a result. This deformation continues until the gasket load is supported. While this works fine the first time – and maybe even the second and the third – eventually the flange becomes both work-hardened and deformed, making it difficult to get good conformation on the subsequent gasket. Ultimately, this increases the potential for leaks. In the following picture, the damage to the groove (“coining” deformation) is clearly visible – a result of the very high seating loads that are generated by an oval ring joint gasket.
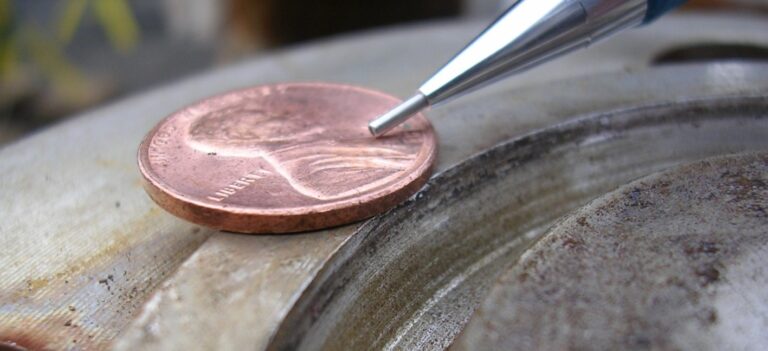
If an incorrect gasket is installed – one that is harder than the flange – this damage to the flange is greatly exacerbated.
Since it doesn’t rely on a single-point contact ring (as the oval does), the octagonal gasket seals much more reliably than the oval gasket, and is far less sensitive to very minor flaws and imperfections in the seating surface. Having said that, manufacturers recommend that the grooves be machined to 63 RMS, whichever type is used.
The greatest advantage of the octagonal gasket is that the exact dimensions of the seating area are known, enabling the user to calculate the exact torque values that will result in a specific, targeted gasket seating stress. This allows the user to put into place more effective bolting protocols that can help – on the one hand – guarantee sufficient gasket stress to prevent leakage, while – on the other – keep from over-tightening the flange, and thereby running the risk of yielding the studs, rotating the flange, or damaging the gasket surface.
Many of our customers – in their effort to improve sealing reliability in all bolted connections – are establishing bolt-up protocols based on gasket seating stress. By switching to octagonal gaskets, these customers can now bring the entire class of ring joint flanges into the same program.
Conclusion: ERIKS encourages the use of octagonal ring joints.